Fluoroethylene vinyl ether (FEVE) resins were developed in Japan in the early 1980’s. It is second-generation fluoropolymer coating with a similar level of durability, weatherability , adhesive force, flexibility, and color and gloss retention as PVDF coatings. The main differences between these two exterior coating technologies is that PVDF resin based coating has a limitation on the maximum gloss, it can achieve of 20%-40%, FEVE coatings on the other hand, can achieve a wider gloss range f 20%-80%. The primary applications for panels sheets coated with FEVE resins are for architectural and outdoor signage, where high gloss and durability are requested.
Raw material:
Base material: high strength aluminum alloy sheet
PE core material: non-toxic low density polyethylene
Surface coating: FEVE coating
Back coating: primer coating
Aluminum | AA1100 AA3003 AA5005 |
Aluminum skin | 0.21mm,0.30mm,0.35mm,0.40mm,0.45mm,0.5mm |
Panel thickness | 3mm,4mm,5mm,6mm |
Panel width | 1220mm,1250mm,1500mm |
Panel length | 2440mm,3050mm,4050mm |
Surface treatment | FEVE |
Colors | 70 colors,RAL & PANTONE colors upon request |
Customers size | accepted |
Glossy | 20%-80% |
Panel width: ±2mm Panel length:±3mm
Panel thickness: ±0.2mm Panel diagonal: ≤5mm
Aluminum sheet thickness: ±0.01mm
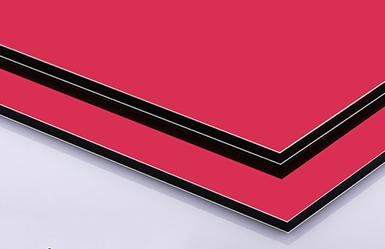
*With high glossy and Vivid colors as PE coating
*With high weather resistant as PVDF coating
*High surface hardness ,Pencil hardness is over 4H
*Special for exterior building and sign industry
1. Wall curtain, Cladding and Facade
2. Hotels and commercial mansions
3. Exterior renovation for old buildings
4. Subway and airports
5. Industry plants and materials,
6. Vehicle and boat materials
Product Properties
Good flatness and fineness
Strong ink absorption
Easy peeling of protective film
High resistance to peeling
Superior weather resistance
Light weight and easy to process
Excellent fire resistance properties
-
Application
-
Application
-
Application
-
Application
-
Application
-
Application
Description | Test standard | FEVE |
Thickness of coating | PVDF paint≥25um | 32um to 36um |
Coating flexibility (T-bend) | Polyester paint≥3T | 3T |
Color different | ΔE≤2.0(follow color sample) | ΔE<1.0 |
Pencil hardness | ≥HB | ≥4H |
Chemical resistance | 5%HCI or 5% NaOH test in 24 hours -No change;ASTM D1308 | No change |
Coating adhesion | ≧1grade for 10*10mm2 gridding test | 1grade |
Resist solvent | No change for 200 times(MEK) | No change |
Boiling water resistance | Coating no tear off for 2 hours | No TEAR OFF |
Peeling strength/stripping strength | Average ≥7N/mm of 180oc peel off for panel with 0.5mm alu.skin | 7N/mm |
Impact test for paint | 50KG.cm impact-paint no split for panel | No split |
Abrasion resistance (L/Mil) | ASTM D968 | 44 |
Temperature resistance | -40℃ to +80℃ temperature without change of color difference and paint peel off,peeling strength average drop rate ≤10% | Change of glossy only,no paint Peel off |
Coefficient of linear Thermal Expansion | 100℃ temperature difference | 2.4mm/m |
Detergent resistance (3%) | ASTM D2248 | No change |
Humidity Resistance (3000hrs,100%RH,100°F) | ASTM D2247 | No change |
Salt spray resistance (3000hrs,5% salt) | ASTM B117 | No change |
Resistance to Staining | 4000h radiate in 800W/m2 in humidity condition,glossiness deviation less grade 2,color difference ≤4.0 | No change |